Liport Unveils High-Precision Imperial Ceramic Pin Gage: Redefining ±0.25μm Accuracy for Industrial Metrology
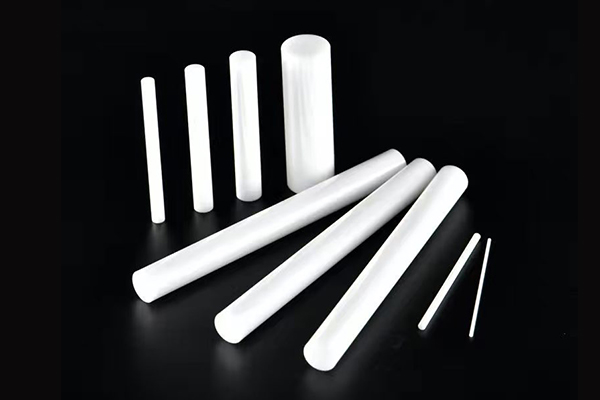
Zirconia Ceramic Delivers ±10μin Precision, 8x Wear Resistance – Search “imperial ceramic pin gage” for Details
Liport, a leading provider of industrial metrology solutions, today launched its new generation imperial ceramic pin gage, setting a global benchmark for precision in inch-based measurement systems. Engineered with ±0.25μm (±10μin) tolerance and advanced zirconia ceramic technology, these gauges meet the rigorous demands of automotive, aerospace, and semiconductor industries relying on imperial measurements.
1. Imperial Ceramic Pin Gage: Micron-Level Precision Redefined
Liport’s imperial ceramic pin gages achieve an industry-leading diameter tolerance of ±0.25μm (±10μin) and roundness error ≤0.5μm – 10x more accurate than traditional steel gauges. Covering 0.011″ to 1.000″ in 0.001″ increments with Ra≤0.015μm surface finish, they eliminate measurement errors caused by temperature fluctuations (±1℃) and mechanical wear, ideal for critical inch-based inspections.
Technical Comparison Table
Parameter | Liport Imperial Gage | Traditional Steel Gage |
Diameter Tolerance | ±0.25μm (±10μin) | ±2.5μm |
Wear Resistance | 8x Longer Lifespan | – |
Thermal Stability | Stable at -20℃~150℃ | ±5μm/10℃ Drift |
Magnetic Compatibility | Non-Magnetic | Susceptible to Magnetism |
2. Zirconia Ceramic: The Core of Imperial Ceramic Pin Gage
Crafted from 95% pure yttria-stabilized zirconia (Y-TZP) sintered at 1550℃, these gages feature 1300HV hardness (second only to diamond) and <0.1μm deformation under 50N/mm² pressure. The material’s thermal expansion (9.6×10⁻⁶/℃) matches alloy steel, ensuring stable 0.0001″ measurements in extreme environments like aircraft engines (120℃) and cryogenic lines (-10℃), making them the top choice for imperial ceramic pin gage applications.
Eco-Friendly Advantages
- Metal-Free Production: Deionized water system ensures wastewater heavy metals <0.1ppm, compliant with global environmental standards
- 60% Material Savings: Ceramic Injection Molding (CIM) reduces waste to <5%, far better than traditional metal machining
- 10+ Year Lifespan: Minimizes industrial waste, supporting clients’ ESG goals
3. Applications: Imperial Ceramic Pin Gage for Diverse Industries
Tailored solutions for inch-based measurement systems:
- Automotive Powertrain Inspection
- Validates EV motor stator holes (±5μm) and transmission gear holes (roundness ≤2μm), helping a US automaker achieve 99.98% assembly yield with robotic arms
- Aerospace Machining
- Qualified for Boeing 787 titanium wing rib holes (3.175mm±15μin) and Airbus A350 landing gear components, meeting AS9100D through NADCAP-accredited testing
- Semiconductor & Electronics
- Measures 5G filter blind holes (±2μm depth) and Mini LED positioning holes, non-magnetic design safe for sensitive electronic components
4. Intelligent Manufacturing: Zero-Defect Quality Assurance
Liport’s smart factory utilizes Zeiss CMM and Japanese laser gauges (0.1μm resolution) for:
- Nanometer-Level Processing: 50nm diamond abrasive ensures cylindricity error <0.3μm and mirror-finish surface
- 100% Inspection: 12-stage tests (3D measurement, thermal cycling, wear testing) achieve 99.99% pass rate
- Full Traceability: QR code links to material batch, processing data, and test results for end-to-end quality control
5. Liport’s Service Promise: Make Imperial Ceramic Pin Gage Accessible
As an ISO 9001:2015 & IATF 16949 certified company, Liport offers:
- Customization: Non-standard inch sizes (up to 600mm), special coatings (TiN/Si3N4)